Automated frozen goods warehouse for Talley’s
One of Talley’s most important sites is their vegetable processing plant near Ashburton, which serves a 4500-hectare growing area between the Rangitata and Rakaia Rivers. In true Talley’s style, every aspect of planting, harvesting, processing, freezing, packing, cold storage and freight is meticulously controlled to ensure Talley’s customers consistently receive nothing but the best.
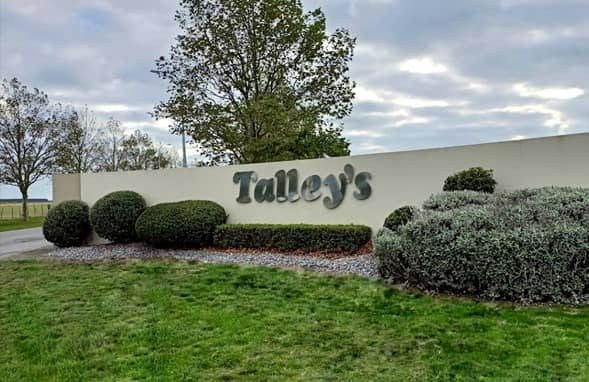
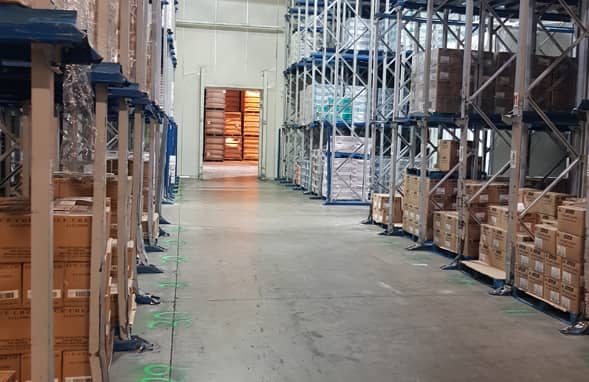
Challenge
Talley’s approached us to design and implement automated materials handling solutions for a new frozen goods warehouse. For them, moving to a fully-automated cool store was the next logical step for their company’s growth.
The greatest challenge with this project was the timing. The new cool store was commissioned just prior and during the Covid-19 lockdown period. As it turned out, this timing was serendipitous. When Covid-19 sent the country spinning into Lockdown, a surge in demand for vegetables presented an opportunity for Talley’s to come to the rescue.
“A lot of vegetables are imported into New Zealand and the importers couldn’t react as fast as we could to Covid. Seeing this, we swapped our factory over from export products to domestic products to meet demand.’ says Aaron Chudleigh, General Manager – Vegetables at Talley’s.
Solution
Working with our Italian partner Automha and local Racking Partner StorePro PHS Innovate’s scope included all the racking, automation equipment and conveyors in and surrounding the Cool store.
The system scans wrapped and labelled pallets and communicates with Talley’s inventory system to retrieve details for the pallet. The system then stores the pallets in rack locations based on Batch and date for optimised future retrieval.
When a truck or container load is needed, Talley’s inventory system communicates with our automated handling system to request specific pallets. Our solution then retrieves and delivers the requested pallets to a designated area for the forklift driver to load into the truck or container.
While Covid-19 lockdowns were a hindrance during the commissioning stage, we found work arounds that enabled us to keep the project moving forward. In fact, we actually hastened implementation to enable Talley’s to lift production to meet New Zealand’s increasing demand for local frozen produce during the pandemic.
Entirely unmanned and free of forklifts, the new system works 24/7 and has given Talley’s the ability to fully utilise the cool store space. The cool store has a capacity of 9204 pallets of finished goods.
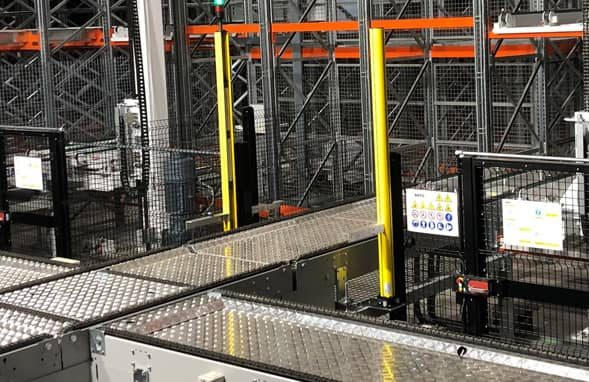
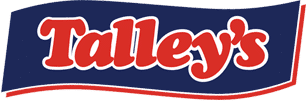

Andre De Beer
Dispatch and Automation Coordinator
Talley’s Limited
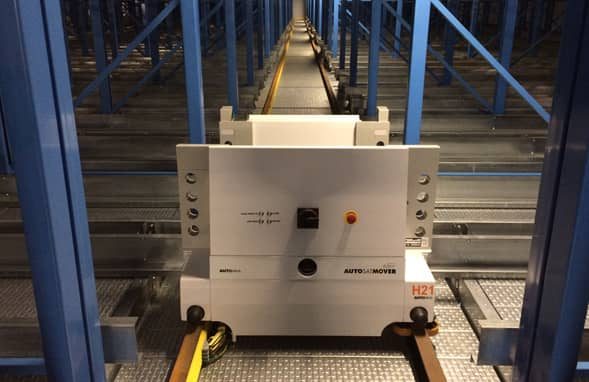
Fact box
- 6 level deep lane storage system
- Automha Movers with onboard satellite shuttle on each level
- Each level treated as a separate safety zone to allow access when required whilst the balance of the system can continue to operate
- Multiple vertical lifts transfer loads to and from all levels and provide built in redundancy
- Warehouse WMS system integrated with the Talley’s ERP system
- Automation remote access setup so PHS Innovate Technicians can provide support if required